Introduction
A diesel generator is an essential component in ensuring a reliable power supply for various industrial applications. The factory acceptance testing (FAT) of a diesel generator is a crucial step in the quality assurance process before deployment in real-world scenarios. This article explores the importance of diesel generators in industrial settings, the key components of a diesel generator, the significance of factory acceptance testing, and the best practices for conducting FAT for diesel generators.
Importance of Diesel Generators in Industrial Settings
In industrial settings, a continuous and reliable power supply is essential for ensuring uninterrupted operations. Power outages can result in significant financial losses due to downtime, disruption of production processes, and damage to equipment. Diesel generators are widely used in industrial applications as a backup power source to mitigate the impact of power outages. These generators provide a reliable source of power during emergencies and serve as a critical component of the overall power infrastructure in factories, manufacturing plants, data centers, and other industrial facilities.
Key Components of a Diesel Generator
A diesel generator is a complex system that comprises several key components working together to generate electrical power. The main components of a diesel generator include:
1. Diesel Engine: The diesel engine is the primary component of a diesel generator responsible for converting the chemical energy of diesel fuel into mechanical energy. The engine drives the generator to produce electricity through the rotation of a shaft connected to an alternator.
2. Alternator: The alternator is a crucial component of the diesel generator that converts the mechanical energy from the engine into electrical energy. It consists of a rotor and stator that generate an alternating current (AC) output.
3. Fuel System: The fuel system of a diesel generator includes a fuel tank, fuel pump, fuel filter, and fuel injectors. The fuel system delivers diesel fuel to the engine for combustion, providing the energy required to power the generator.
4. Cooling System: The cooling system of a diesel generator regulates the temperature of the engine to prevent overheating and ensure optimal performance. 200kw diesel generator for sale includes a radiator, cooling fan, thermostat, and coolant circulation system.
5. Control Panel: The control panel is the interface through which the operator can start, stop, and monitor the operation of the diesel generator. It displays key parameters such as voltage, current, frequency, and engine status, allowing for real-time monitoring and control.
Significance of Factory Acceptance Testing (FAT)
Factory acceptance testing (FAT) is a critical step in the quality assurance process for diesel generators before they are deployed in industrial applications. FAT involves testing and verifying the performance, functionality, and compliance of the generator with the specified requirements and standards. The primary objectives of FAT for a diesel generator include:
1. Verification of Specifications: FAT ensures that the diesel generator meets the specifications and performance criteria outlined in the design and engineering documents. It validates that the generator is capable of delivering the required power output, voltage regulation, frequency stability, and other key parameters.
2. Functional Testing: FAT involves testing the functionality of the diesel generator under various operating conditions to ensure that all components are working correctly. This includes testing the starting system, fuel system, cooling system, electrical connections, and control panel functionality.
3. Performance Evaluation: FAT evaluates the performance of the diesel generator by conducting load tests to simulate different operating conditions and verify the generator's ability to handle varying loads. Performance testing helps identify any issues related to power output, voltage regulation, frequency control, and overall efficiency.
4. Compliance with Standards: FAT ensures that the diesel generator complies with relevant industry standards, regulations, and safety requirements. It verifies that the generator is designed and manufactured according to established guidelines to ensure safe and reliable operation in industrial environments.
Best Practices for Conducting FAT for Diesel Generators
To ensure the success of factory acceptance testing for diesel generators, it is essential to follow best practices and guidelines to conduct thorough and comprehensive testing. Some of the key best practices for conducting FAT for diesel generators include:
1. Preparation and Planning: Proper preparation and planning are essential for conducting successful FAT for a diesel generator. This includes reviewing the project specifications, preparing test procedures, scheduling resources, and coordinating with all stakeholders involved in the testing process.
2. Test Documentation: Documenting test procedures, test results, and observations is crucial for tracking the progress of FAT and ensuring that all requirements are met. Detailed test reports provide a record of the testing process and serve as a reference for future troubleshooting and maintenance.
3. Functional Testing: Conduct comprehensive functional testing of all components of the diesel generator, including the engine, alternator, fuel system, cooling system, and control panel. Verify that all systems are operating correctly and that there are no malfunctions or defects that could affect the performance of the generator.
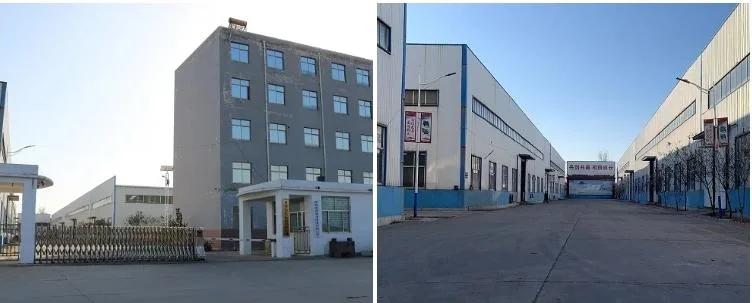
4. Load Testing: Perform load tests on the diesel generator to evaluate its performance under varying load conditions. Test the generator at different load levels to assess its power output, voltage regulation, frequency stability, and response to load changes.
5. Safety Precautions: Prioritize safety during FAT by following proper safety procedures and precautions to prevent accidents and ensure the well-being of personnel involved in the testing process. Adhere to safety guidelines for handling fuel, electrical connections, moving parts, and other potential hazards.
6. Quality Assurance: Implement quality assurance measures to ensure that the diesel generator meets the highest standards of quality and reliability. Verify that the generator is constructed with high-quality materials, components, and workmanship to withstand the rigors of industrial operation.
Conclusion
Diesel generators play a vital role in ensuring a reliable power supply for industrial applications, serving as a backup power source during emergencies and power outages. The factory acceptance testing (FAT) of a diesel generator is a crucial step in the quality assurance process to verify its performance, functionality, and compliance with specifications and standards. By following best practices for conducting FAT, manufacturers and operators can ensure that diesel generators meet the highest standards of quality and reliability, providing uninterrupted power supply for industrial operations.